Introduction: Old School Meets High Tech
When we talk about modern electronics manufacturing, Surface Mount Technology (SMT) often steals the spotlight. But behind the scenes, another technique—wave soldering—still plays a crucial supporting role. While SMT is ideal for small, lightweight components, wave soldering is often the go-to choice for through-hole and hybrid assemblies.
In this article, we’ll explore what wave soldering is, how it works, and why it's far from outdated. More importantly, we’ll show you how it complements SMT in high-efficiency electronics production.
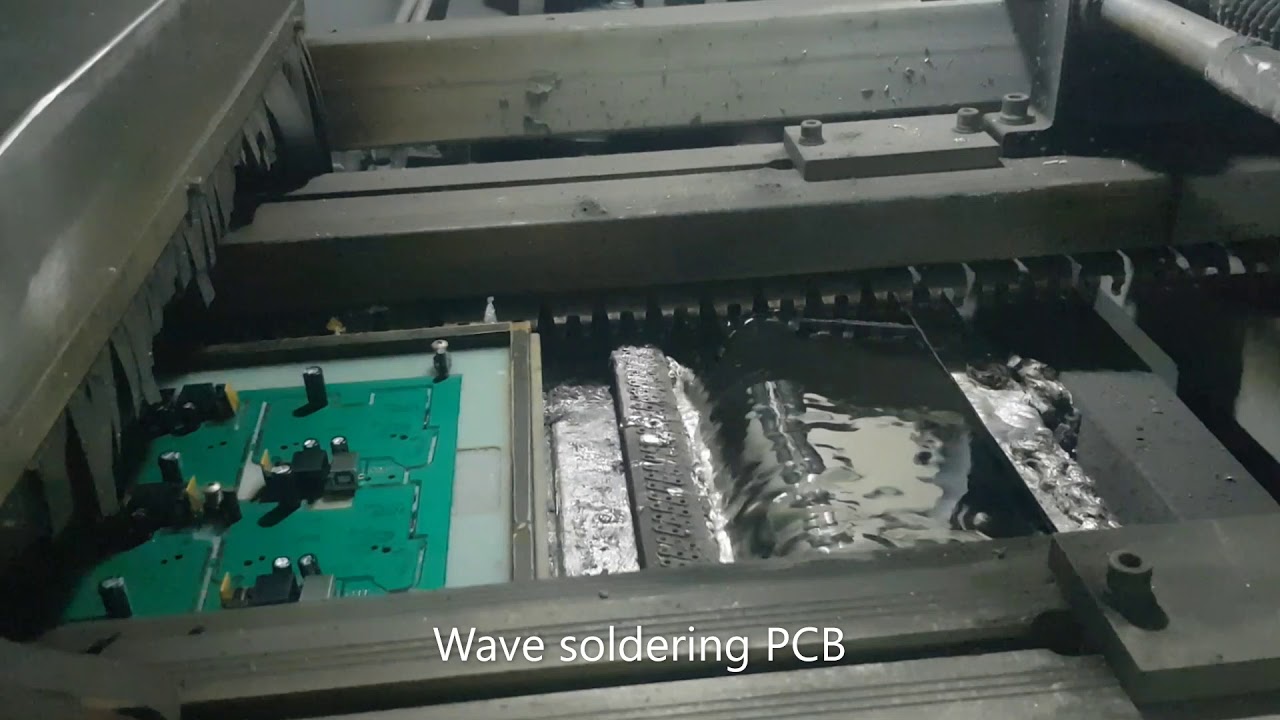
1. What Is Wave Soldering? A Quick Overview
Wave soldering is a bulk soldering process used to attach through-hole electronic components to a printed circuit board (PCB). The entire PCB is passed over a wave of molten solder, which creates strong, reliable joints in a single sweep.
- Typically used for through-hole components
- Suitable for high-volume production
- Offers strong mechanical bonds
In contrast to SMT, which places components on the surface and uses a reflow oven, wave soldering involves immersing the bottom of the PCB into a moving wave of solder.
2. Wave Soldering vs. SMT: A Perfect Match
While SMT has taken over much of electronics manufacturing, wave soldering still holds its ground in specific scenarios. In fact, they often work together in a complementary fashion.
Feature | SMT | Wave Soldering |
---|---|---|
Component Type | Surface-mount | Through-hole |
Automation Level | Highly automated | Semi-automated/manual |
Ideal For | Compact circuits | Heavy-duty connectors |
Temperature Control | Precision via reflow oven | Bulk solder wave |
Best Used In | Phones, laptops, IoT | Automotive, power supplies |
3. How Wave Soldering Works: A Deeper Dive
Let’s break down the wave soldering process step by step. It’s surprisingly elegant in its simplicity.
- Flux Application – The bottom of the PCB is sprayed with flux to clean the metal surfaces.
- Preheating – The board is preheated to prevent thermal shock and activate the flux.
- Solder Wave – The PCB passes over a wave of molten solder, which bonds the component leads.
- Cooling – The solder solidifies, locking the components in place.
Advantages: Cost-effective, strong joints, ideal for transformers/connectors.
4. Market Trends: Who’s Still Using Wave Soldering?
Despite SMT's dominance, wave soldering remains essential in several industries. The global demand is steady, especially in sectors requiring mechanical strength or legacy components.
Industry | Usage Share | Notes |
---|---|---|
Automotive Electronics | 34% | Robust connections needed for vibration resistance |
Power Supply Units | 25% | High current paths require strong joints |
Industrial Equipment | 18% | Older designs still use through-hole parts |
Consumer Electronics | 13% | Mostly hybrid boards |
Others | 10% | Medical, military, aerospace, etc. |
5. FAQs About Wave Soldering
- Q1: Is wave soldering outdated?
A: No. It’s still essential for high-strength or legacy components. - Q2: Can I use wave soldering for SMT parts?
A: Not recommended. SMT uses reflow soldering. - Q3: Is wave soldering cheaper than SMT?
A: Often yes, for large through-hole assemblies. - Q4: Does wave soldering work on both PCB sides?
A: Typically one side only. Use selective soldering for both sides. - Q5: What’s its biggest advantage?
A: Speed and strength in soldering multiple pins at once.
Conclusion: Why Wave Soldering Still Matters
While new technologies continue to emerge, wave soldering remains a staple in PCB assembly. It may not be as flashy as SMT, but it’s incredibly reliable, fast, and perfect for specific tasks SMT can’t handle.
In today’s hybrid manufacturing environment, combining SMT for speed and miniaturization with wave soldering for strength and legacy compatibility ensures products are built better and smarter.
So, next time you see a sturdy power connector or a durable automotive PCB—know that wave soldering probably had something to do with it.