PCB Manufacturing & Assembly Capabilities
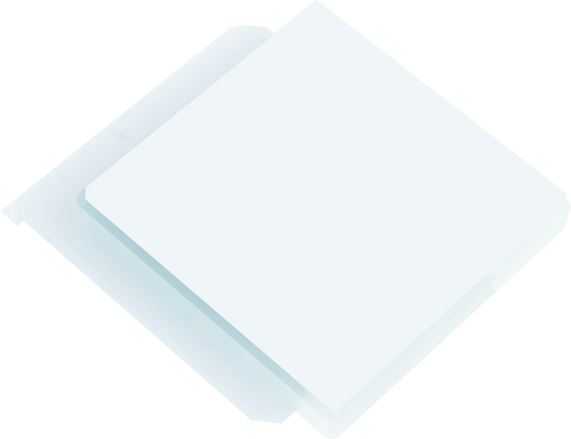
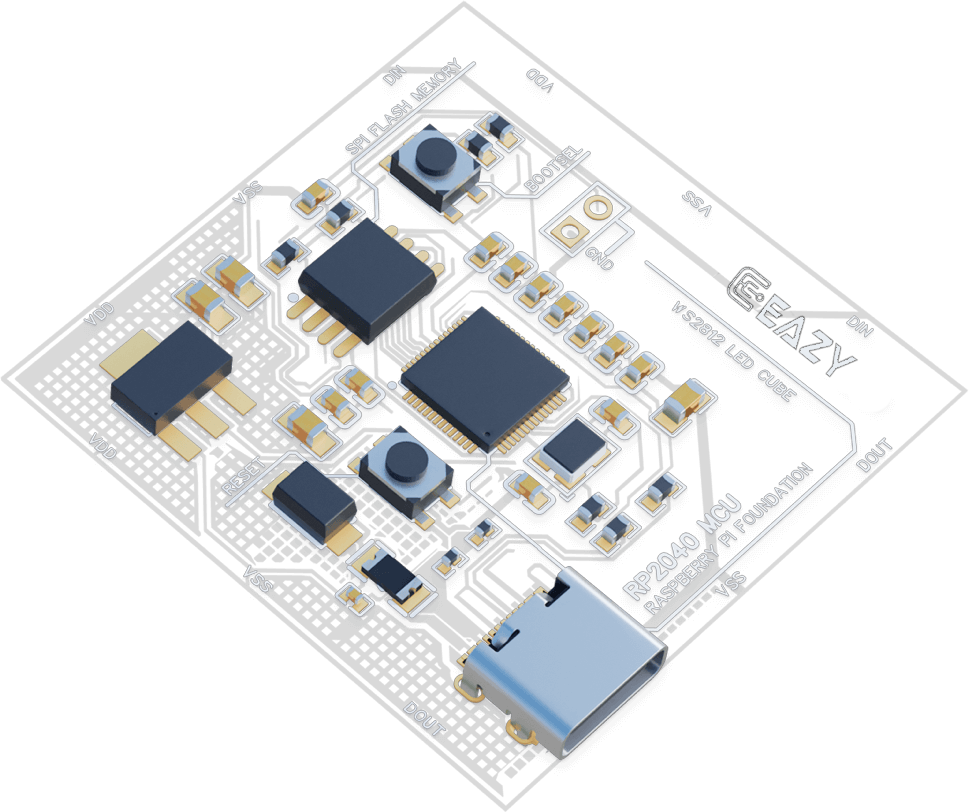
Features | Capability | Description | Patterns |
---|---|---|---|
Layer count | 1-32 Layers | The number of copper layers in the PCB | |
Controlled Impedance | 4/6/8/10/12/14/16/18/20/.../32 layers |
User Guide to the EAZYPCB Impedance Calculator EAZYPCB Impedance Calculator |
|
Material | FR-4 | Grade A laminates from suppliers including Nan Ya, KB, Shengyi and etc. | |
Aluminum-Core | 1-layer Aluminum-core PCBs | ||
Copper-Core | 1-layer copper-core PCBs with direct heatsink contacts (≥ 1 × 1 mm) | ||
RF PCB | 1 oz copper, 2-layer RF PCBs with Rogers and PTFE cores | ||
FR-4 Dielectric Constants | 4.5 (2-Layer PCB) |
7628 Prepreg 4.4 3313 Prepreg 4.1 2116 Prepreg 4.16 |
|
Maximum Dimensions |
FR4 PCB: 670 × 600 mm Rogers / PTFE Teflon PCB: 590 × 438 mm Aluminum PCB: 602 × 506 mm Copper PCB: 480 × 286 mm |
These limits apply to PCBs with thickness ≥ 0.8 mm. The thinner FR4 PCBs are 500 × 600 mm maximum. 2-layer FR4 PCBs can reach a maximum size of 1020 × 600 mm. |
|
Minimum Dimensions | Regular: 3 × 3 mm. Castellated / Plated Edges: 10 × 10 mm. | These limits apply to PCBs with thickness ≥ 0.6 mm. Manual review required for thinner PCBs. Panelization is recommended for small-sized boards. | |
Dimension Tolerance | ±0.1mm | ±0.1mm(Precision) and ±0.2mm(Regular) for CNC routing, and ±0.4mm for V-scoring | |
Thickness | 0.4 - 4.5 mm | Thickness for FR4 are: 0.4/0.6/0.8/1.0/1.2/1.6/2.0 mm (2.5 mm and above are for 12+ layer PCBs only) | |
Thickness Tolerance (Thickness≥1.0mm) | ± 10% | e.g. For the 1.6mm board thickness, the finished board thickness ranges from 1.44mm(T-1.6×10%) to 1.76mm(T+1.6×10%) | |
Thickness Tolerance (Thickness<1.0mm) | ± 0.1mm | e.g. For the 0.8mm board thickness, the finished board thickness ranges from 0.7mm(T-0.1) to 0.9mm(T+0.1). | |
Finished Outer Layer Copper | 1 oz / 2 oz (35um / 70um) | Finished copper weight of outer layer is 1oz or 2oz. | |
Finished Inner Layer Copper | 0.5 oz / 1 oz / 2 oz (17.5um / 35um / 70um) | Finished copper weight of inner layer is 0.5oz by default. | |
Soldermask | Green, Purple, Red, Yellow, Blue, White, and Black. | We use LPI (Liquid Photo Imageable) solder mask. This is the most common type of mask used today. Heat-cured ink soldermask is usually found on low-cost, single-sided PCBs. | |
Surface Finish | HASL (leaded /lead-free), ENIG, OSP (copper core boards only) | FR4 has all three finishes available, 6+ layers and RF boards only have ENIG. Aluminum core boards only have HASL. Copper core boards only have OSP. |
Features | Capability | Description | Patterns |
---|---|---|---|
Drill Diameter |
1-layer: 0.3 – 6.3 mm
2-layer: 0.15 – 6.3 mm Multilayer: 0.15 – 6.3 mm |
Holes with diameter ≥ 6.3 mm are CNC routed from a smaller drilled hole.
Min. drill diameter for 2- or more-layer PCBs is 0.15 mm (more costly) Min. drill diameter for aluminum-core PCBs is 0.65 mm Min. drill diameter for copper-core PCBs is 1.0 mm |
|
Hole size Tolerance (Plated) |
Through-holes: +0.13 / -0.08 mm
Press-fit holes: ±0.05 mm (multilayer EMI boards only – mention the specific holes in PCB Remark) |
e.g. for the 0.6mm hole size, the finished hole size between 0.52mm to 0.73mm is acceptable.
|
|
Hole size Tolerance (Non-Plated) |
±0.2mm
|
e.g. for the 1.00mm Non-Plated hole, the finished hole size between 0.80mm to 1.20mm is acceptable.
|
|
Average Hole Plating Thickness |
18μm
|
||
Blind/Buried Vias |
Not supported
|
Currently we don't support Blind/Buried Vias, only make through holes.
|
|
Min. Via hole size/diameter |
0.15mm / 0.25mm
|
1-layer (NPTH only): 0.3 mm hole size / 0.5 mm via diameter
2-layer: 0.15mm hole size / 0.25mm via diameter Multilayer: 0.15 mm hole size / 0.25 mm via diameter ① Via diameter should be 0.1mm(0.15mm preferred) larger than Via hole size. ② Preferred Min. Via hole size: 0.2mm |
|
Min. Non-plated holes |
0.50mm
|
Please draw NPTHs in the mechanical layer or keep out layer.
|
|
Min. Plated Slots |
0.5mm
|
The minimum plated slot width is 0.5mm, which is drawn with a pad.
|
|
Min. Non-Plated Slots |
1.0mm
|
The minimum Non-Plated Slot Width is 1.0mm, please draw the slot outline in the mechanical layer(GM1 or GKO)
|
|
Via Hole-to-Hole Spacing |
0.2mm
|
|
|
Pad Hole-to-Hole Spacing |
0.45mm
|
|
|
Min. Castellated Holes |
0.60mm
|
Castellated holes are metalized half-holes on PCB edges, commonly used on daughter boards to be soldered onto carrier PCBs.
① Hole diameter (Ø): ≥ 0.6 mm ② Hole to board edge (L): ≥ 1 mm ③ Hole to hole (D): ≥ 0.6 mm ④ Min. PCB size: 10 × 10 mm ⑤ Min. PCB thickness: 0.6 mm |
|
Plated Edges |
10 x 10mm
|
Plated edges are copper-plated and ENIG treated, HASL is not supported.
① Min. PCB size: 10 × 10 mm ② Min. PCB thickness: 0.6 mm ③ At least 3 breaks (more for larger PCBs) in the edge plating are required for support tab connections |
|
Rectangular Holes / Slots |
Not supported
|
Rectangular holes and slots without rounded corners are not supported.
|
|
Features | Capability | Description | Patterns |
---|---|---|---|
Min. track width and spacing (1 oz) |
0.10 / 0.10 mm (4 / 4 mil)
|
1- and 2-layer: 0.10 / 0.10 mm (4 / 4 mil)
Multilayer: 0.09 / 0.09 mm (3.5 / 3.5 mil), 3 mil is acceptable in BGA fan-outs. |
|
Min. track width and spacing (2 oz) |
0.16 / 0.16 mm (6.5 / 6.5 mil)
|
2-layer: 0.16 / 0.16 mm (6.5 / 6.5 mil)
Multilayer: 0.16 / 0.20 mm (6.5 / 8 mil) |
|
Track width tolerance |
±20%
|
e.g. For a 0.1 mm track, the finished track width ranges from 0.08 and 0.12 mm.
|
|
PTH annular ring |
≥0.20mm
|
2-layer:
1 oz: Recommended 0.25 mm or above; absolute minimum 0.18 mm 2 oz: 0.254 mm or above Multilayer: 1 oz: Recommended 0.20 mm or above; absolute minimum 0.15 mm 2 oz: 0.254 mm or above |
|
NPTH pad annular ring |
≥0.45mm
|
Recommended 0.45 mm or more. This is to allow a 0.2 mm ring of copper to be removed around the hole for the sealing film to attach. Pad sizes smaller than the recommended value can result in the annular ring being very thin or completely missing.
|
|
BGA |
0.25mm
|
① BGA pad diameter ≥ 0.25 mm
② BGA pad to trace clearance ≥ 0.1 mm (min. 0.09 mm for multilayer boards) ③ Vias can be placed within BGA pads using filled and plated-over vias |
|
Trace coils |
0.15/0.15mm
|
Minimum trace width/clearance: 0.15/0.15mm, when traces are covered by solder mask (1oz)
Minimum trace width/clearance: 0.25/0.25mm, when traces are NOT covered by solder mask (1oz). ENIG only(high risk of short circuit with HASL) |
|
Hatched grid width and spacing |
0.25 mm
|
|
|
Same-net track spacing |
0.25mm
|
|
|
Inner layer via hole to copper clearance |
0.2mm
|
|
|
Inner layer PTH pad hole to copper clearance |
0.3mm
|
||
Pad to track clearance |
0.1mm
|
Min. 0.1 mm (stay well above if possible). Min. 0.09 mm locally for BGA pads
|
|
SMD pad to pad clearance (different nets) |
0.15mm
|
More details of SMD pad spacing: SMD Components Minimum Spacing
|
|
Via hole to Track |
0.2mm
|
|
|
PTH to Track |
0.25mm
|
0.35mm is recommended, minimum 0.25mm
|
|
NPTH to Track |
0.2mm
|
|
Flexible PCB Capabilities
Category | Features | Capability | Description |
---|---|---|---|
Layer Count
|
1 layer,2 layers
|
The number of copper layers in the FPC
|
Rigid-flex PCBs are not yet supported.
|
FPC Stack-Up
|
Single-Sided
|
FPC with copper and coverlay on the same one side only. Inner PI thickness: 25 μm
|
|
Double-Sided
|
FPC with copper on both sides. Inner PI thickness: 25 μm
|
|
|
Dimensions
|
Maximum Dimensions
|
Regular: 234 × 490 mm
|
Absolute limit of 250 × 500 mm allowed with mandatory handling edges – confirm with customer support before ordering
|
Minimum Dimensions
|
No limit, but FPCs whose dimension is smaller than 20 × 20 mm are best panelised
|
||
FPC Finished Thickness
|
Single-sided: 0.07 / 0.11 mm Double-sided: 0.11 / 0.12 / 0.2 mm |
The thickness of the finished FPC excluding any stiffeners(If the measured area has no copper or coverlay, the finished thickness will be reduced.)
|
|
Outer Layer Copper Weight
|
Single-sided: 18 μm (0.5 oz), 35 μm (1 oz) Double-sided: 12 μm (0.33 oz), 18 μm (0.5 oz), 35 μm (1 oz) |
The thickness of copper on the FPC
|
|
Type of Process
|
Dry film process with LDI (laser direct image) exposure technology
|
LDI provides higher accuracy than traditional LED exposure. The machines also support automatic alignment based on board size to eliminate pad offset issues.
|
|
Surface Finish
|
ENIG. Thickness: 1u" / 2u"
|
ENIG deposits a nickel-gold coating on exposed pads to prevent oxidation.
|
|
Thickness with Stiffener
|
Thickness with Stiffener = FPC Thickness + Stiffener Thickness
|
||
FPC Thickness Tolerance
|
±0.05 mm
|
Additional tolerance exists for stiffeners. Thicker stiffeners have larger tolerances.
|
|
Holes
|
Hole Diameter
|
0.15-6.5 mm
|
The recommended maximum diameter for PTHs is 5 mm, if bigger may cause risks to production
|
Diameter Tolerance
|
±0.08 mm
|
Example: A 1.00 mm designed diameter is allowed to yield any physical diameter between 0.92-1.08 mm.
|
|
Minimum Plated Slot
|
0.50 mm
|
|
|
Minimum Non-Plated Slot
|
Not limited
|
At least 0.2 mm copper clearance is required around non-plated slots.
|
|
Castellated holes are plated half-holes on the edge of an FPC. Most often used for press-soldered connectors. ① Castellated hole diameter: ≥ 0.3 mm ② Castellated hole to board edge: ≥ 0.5 mm ③ Castellated hole to hole: ≥ 0.4 mm |
|
||
Min. Via hole size/diameter
|
0.15 mm (Via hole size)/ 0.35 mm (Via diameter) ① Annular ring: 0.1 mm minimum, 0.125 mm recommended ② Recommended via size: 0.3 mm inner, 0.55 mm outer |
|
|
Traces
|
Annular Ring for PTH
|
≥ 0.25 mm recommended, absolute limit: 0.18 mm
|
|
Minimum Trace Width/Spacing (1 oz)
|
① 12 μm (0.33 oz) copper: 3/3 mil (absolute limit 2/2 mil – avoid if possible) ② 18 μm (0.5 oz) copper: 3.5/3.5 mil ③ 35 μm (1 oz) copper: 4/4 mil These are regular capabilities. Contact customer support for custom capability requirements. |
|
|
Trace Width Tolerance
|
±20%
|
Example: A 0.10 mm designed trace width is allowed to yield any physical width between 0.08-0.12 mm.
|
|
Pad-to-Trace Clearance
|
① Via ring to trace: ≥ 0.1 mm (more whenever possible) ② Exposed pad to trace:≥ 0.15 mm (more whenever possible) |
|
|
NPTH to Copper Clearance
|
≥ 0.20 mm
|
The clearance from an NPTH to traces, pads, and copper pours
|
|
BGA
|
① BGA pad diameter: ≥ 0.25 mm ② BGA pad to trace clearance: ≥ 0.2 mm |
|
|
Coverlay/ Soldermask |
Coverlay Color
|
Yellow / Black / White
|
Yellow is recommended
|
Coverlay Opening
|
Coverlay expansion (one-sided): 0.1 mm Coverlay opening to trace clearance: ≥ 0.15 mm (more whenever possible) |
|
|
Via covering
|
Recommended to keep coverlay over vias
|
||
Coverlay Thickness
|
① PI: 12.5 μm, glue: 15 μm (on 12/18 μm copper) ② PI: 25 μm, glue: 25 μm (on 35 μm copper) |
|
|
Minimum solder bridge width
|
0.5 mm minimum, i.e. solder bridge narrower than 0.5 mm will be removed. Contact customer support for any non-standard requirements.
|
|
|
Silkscreen
|
Character Height
|
≥ 1mm (More in case of complex patterns or knock-out text)
|
|
Character Line Width
|
≥ 0.15mm (Narrower lines do not print well)
|
||
Character to Pad Clearance
|
≥ 0.15mm (Any silkscreen closer to a pad than this will be clipped)
|
||
FPC Outline
|
Laser Outline
|
① Copper to board edge ≥ 0.3mm ② Copper to slots ≥ 0.3mm ③ Outline tolerance: ±0.1 mm (±0.05 mm upon request) |
|
Gold Finger Pad to Board Edge Clearance
|
0.2 mm. Gold fingers will be cut back if exceeding this clearance to avoid damage during laser cutting the outline. Castellated pads are exempt from this clearance.
|
|
|
Panels (See FPC Panel Design Guide)
|
① Spacing between boards is commonly 2 mm. For boards with metal stiffeners use 3 mm instead. ② Handling edges of width 5 mm required on all four sides. Copper pour is required on these edges, with 1 mm clearance around fiducials and 0.5 mm clearance around tooling holes. ③ Fiducials: 1 mm; tooling holes: 2 mm; Fiducial centre to board edge: 3.85 mm. Add four fiducials with one offset by 5 mm or more to aid orientation. ④ Support tab width: 0.7-1.0 mm ⑤ Maximum panel size: 234 × 490 mm |
|
|
Stiffeners (Detailed Introduction)
|
PI Stiffener
|
Thickness options: 0.1 mm, 0.15 mm, 0.20 mm, 0.225 mm, 0.25 mm
|
PI stiffeners are most often used with gold finger connectors. For example if the connector needs to be 0.3 mm thick on a 0.11 mm FPC, a 0.225 mm stiffener thickness is most suitable.
|
FR4 Stiffener
|
Thickness options: 0.1 mm, 0.2 mm
|
FR4 is usually only used on low-end products because it is prone to chipping. Avoid if possible.
|
|
Stainless Steel Stiffener
|
Thickness options: 0.1 mm, 0.2 mm, 0.3 mm
|
Steel stiffeners cost more but have excellent flatness and do not easily deform. This makes them good as support under SMD components. Note that since steel is slightly magnetic it should not be used with hall effect sensors or similar components.
|
|
3M Tape
|
3M9077 (0.05 mm thick; heat-resistant) 3M468 (0.13 mm thick; not heat-resistant) |
Usually used to secure FPCs after assembly
|
|
EM Shielding Film
|
18 μm thick, black. Helps lower EMC. The recommended practice is to add soldermask openings over edge guard rails to electrically connect them to the shield films.
|
|
|
Design Considerations
|
Impedance Calculation
|
Core polyimide εr: 3.3 Coverlay εr: 2.9 Core polyimide thickness: 25 μm |
Impedance measurement and control are not yet supported. Traces are only controlled for width and the customer is responsible for choosing trace widths to achieve their impedance requirements.
|
Other FPC Software
|
For compatibility on the layer types, include the outlines of the coverlay openings, stiffener outlines, and any other features in the design files. These should be included as separate layers in the Gerber output.
|
||
Other Design Constraints
|
Same requirements as rigid PCBs in terms of holes, traces, clearances, and silkscreen.
|
||
Gerber File Naming Convention
|
We recommend using standard Gerber file extensions as listed in the design guidelines. If you use non-standard file extensions we will still process your order but the risk of mistakes in layer stackup increases and processing time may be longer.
|
READY TO GET STARTED?
Contact
805, Block A, Guangming Centre, No. 2, Chuangming Road, Yongning Street, Zengcheng District, Guangzhou, China
- op@eazypcb.com
- Eazypcb
- +86 13342868540